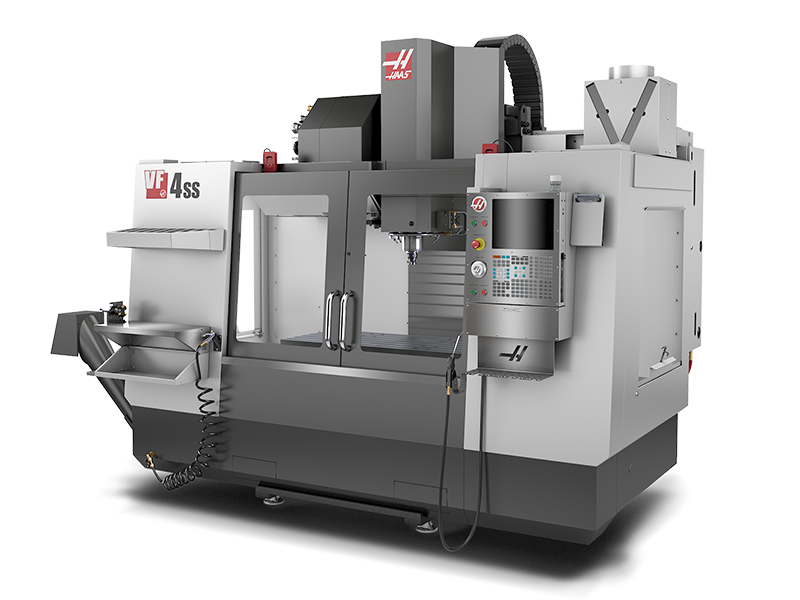
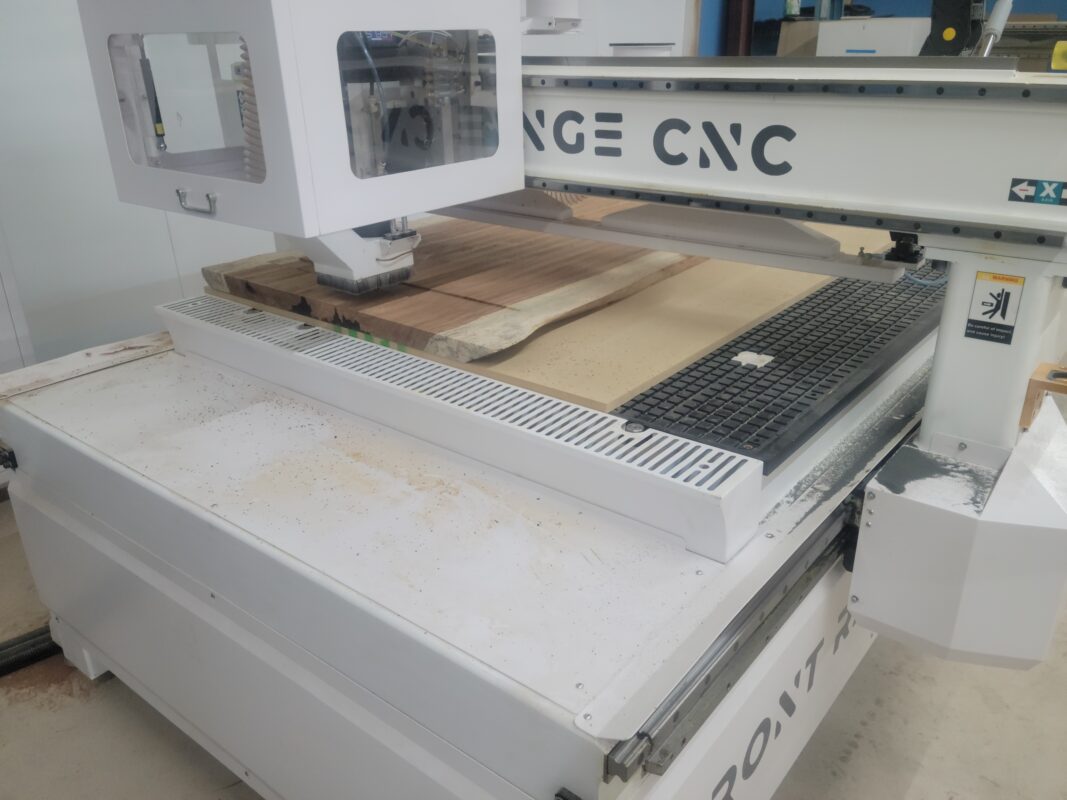
CNC routers and CNC mills are both machines used for cutting materials. Although they share some similarities, there are distinct differences between the two in terms of their design, functionality, and applications. It is important to select the correct machine based on your part size and floor space.
Design and Construction:
CNC routers typically have a gantry-style design, where the cutting spindle moves along the X and Y axes, while the workpiece remains stationary on the bed. The Z-axis provides the spindle’s vertical movement. CNC routers are generally built with lightweight materials and have a more flexible frame structure. You will also see a moving table setup where the bridge is fixed and the table “shuttles” in and out. This can provide additional rigidity and clearance in most router style setups, but it comes at the expense of floor space.
CNC mills tend to have a more rigid and heavy-duty construction, designed to handle higher cutting forces. The cutting spindle in a CNC mill moves along the Z-axis, while the workpiece, mounted on a movable table, moves along the X and Y axes. Mills often utilize an enclosed work envelope that allows them to utilize coolant to help with chip evacuation.
Cutting Forces and Rigidity:
CNC mills are designed to handle higher cutting forces compared to CNC routers. The rigid and robust construction of CNC mills allows them to perform heavy-duty milling operations, such as cutting harder materials like steel, and achieve higher accuracy.
CNC routers are better suited for cutting softer materials like wood, plastic, or foam. Their lightweight construction is not designed for high cutting forces or for handling hard materials.
Spindle Speed and Power:
CNC routers typically have high-speed spindles that can operate at speeds up to 20,000 RPM or even higher, which is ideal for cutting softer materials with a clean finish. However, they often have lower power compared to CNC mills. Their torque curve is much lower and they excel at fast, light cuts.
CNC mills have higher HP spindles that operate at lower speeds, typically ranging from 1,000 to 10,000 RPM. This makes them suitable for cutting harder materials and performing more demanding operations, such as drilling and tapping. They have a different torque curve better suited to aggressive, deep cuts.
Applications: CNC routers are mainly used for woodworking, sign-making, furniture-making, and cutting non-metallic materials like plastics and foam. They are ideal for applications that require high-speed cutting and intricate patterns. Any material that comes in sheet sizing (4’x8’, 5’x10’, etc…) are ideal for a CNC router as the vacuum hold down makes cutting these extremely efficient.
CNC Mills are used primarily in metalworking on repeatable large part runs where the fixturing can be done on a vice or a tombstone setup. Mills typically do not utilize a vacuum bed.