Production Line Automation: Custom Manufacturing Solutions
Elevate Your Manufacturing to World-Class Efficiency
Tailored automation systems designed for your highest-volume production needs at half the cost of European alternatives
Customized Automation for Maximum Throughput
We design and implement complete production automation systems for manufacturers who demand the highest levels of efficiency and throughput. Our solutions integrate multiple CNC machines, automated material handling, and intelligent labeling systems to create a continuous production flow tailored specifically to your manufacturing requirements.
Unlike one-size-fits-all solutions, our Production Line Automation approach begins with your unique production challenges and builds a system to solve them at a fraction of the cost of European alternatives.
Multi-Machine CNC Integration
Synchronized operation of multiple CNC routers with shared material handling
- ✓ Continuous operation with synchronized workflows
- ✓ Upstream labeling for accurate part tracking
- ✓ Automated loading/unloading tables
- ✓ Shared material stacks for maximum efficiency
- ✓ Production increases of 250-400% over single machines
Automated Storage & Retrieval
Intelligent crane systems for vertical space optimization and continuous material flow
- ✓ Automated crane material handling
- ✓ Real-time inventory management
- ✓ Optimized material selection and usage
- ✓ Dramatic floor space reduction
- ✓ Capability for 24/7 lights-out operation
USA-Based Support at Half the European Cost
Our advanced automation systems provide the same capabilities as European solutions at 40-60% lower cost, with all design, implementation, and support based in the USA. We deliver world-class automation without the premium price tag or overseas support complications.
Key Components of Production Line Automation
Synchronized Multi-CNC Systems
Multiple CNC routers working in concert with shared material handling systems enable continuous operation. While one machine is cutting, another can be loading/unloading, eliminating bottlenecks and downtime while dramatically increasing throughput.
Automated Crane Storage Systems
Our vertical storage solutions with automated cranes maximize your facility's cubic footage, storing materials overhead and delivering them precisely when needed. This eliminates manual material handling, reduces labor costs, and enables 24/7 operation.
Intelligent Upstream Labeling
Advanced labeling systems mark materials before they reach the CNC machines, enabling accurate tracking throughout production. This eliminates errors, improves quality control, and allows for precise production scheduling across multiple machines.
End-to-End Integration
From CAD/CAM software to final assembly, our automation systems provide complete integration of your production workflow. Material selection, nesting, cutting, labeling, sorting, and inventory management all function as a cohesive system.
Customized Control Software
Our proprietary control software provides real-time monitoring and management of your entire production line. Intuitive dashboards display productivity metrics, material usage, maintenance requirements, and production schedules for complete oversight.
Scalable System Architecture
Our automation solutions are designed with future growth in mind. Start with essential components and expand capabilities as your production needs evolve. The modular approach allows for strategic investment in automation over time.
Intelligent Production Workflow
See a complete Production Line Automation system in action, seamlessly handling materials from storage to finished product
Automated Material Selection & Retrieval
The system automatically selects optimal materials from vertical storage based on job requirements. Crane systems retrieve sheets and deliver them to the labeling station without manual intervention.
Intelligent Upstream Labeling
Before reaching CNC machines, materials are precisely labeled with part information, job details, and tracking data. This upstream labeling ensures all parts are properly identified throughout the production process.
Synchronized Multi-Machine Processing
Multiple CNC routers work simultaneously, sharing the same material stack. While one machine is cutting, another handles loading/unloading operations, creating a continuous flow of production with minimal downtime.
Automated Sorting & Assembly Preparation
Completed parts are automatically sorted and organized for the next production phase. The system tracks each component, ensuring accurate assembly and minimizing errors in downstream processes.
Real-Time Production Analytics
Throughout the entire process, our control software provides comprehensive analytics on throughput, material usage, machine performance, and production efficiency, allowing for continuous optimization.
Tailored Solutions for High-Volume Industries
Cabinet Manufacturing
Transform your cabinet production with automated nesting, cutting, drilling, and sorting. Our systems handle everything from raw sheet goods to ready-to-assemble components with minimal human intervention.
Furniture Production
Compete with overseas manufacturers by automating your furniture production line. From panels to complex components, our systems deliver precision, consistency, and dramatic labor savings.
Building Components
Scale your production of architectural elements, millwork, and building components with automated material handling, labeling, and multi-machine processing for maximum throughput.
Aerospace Manufacturing
Meet demanding aerospace tolerances and production schedules with our precision automation systems. Ensure complete traceability and consistency across high-value components.
No matter your industry, our systems are custom-designed for your specific production requirements, material types, and throughput needs.
Production Automation ROI
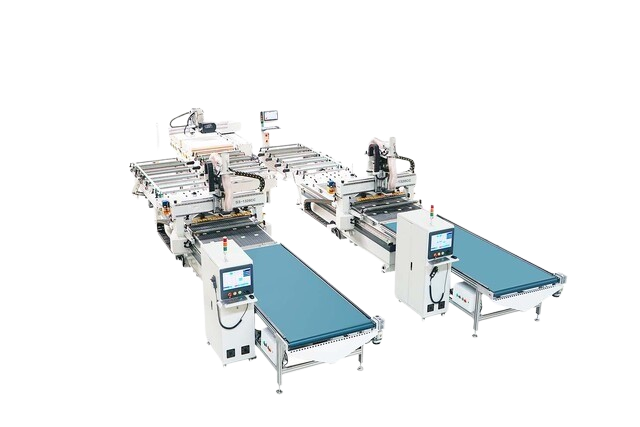
Dual CNC router system with shared infeed
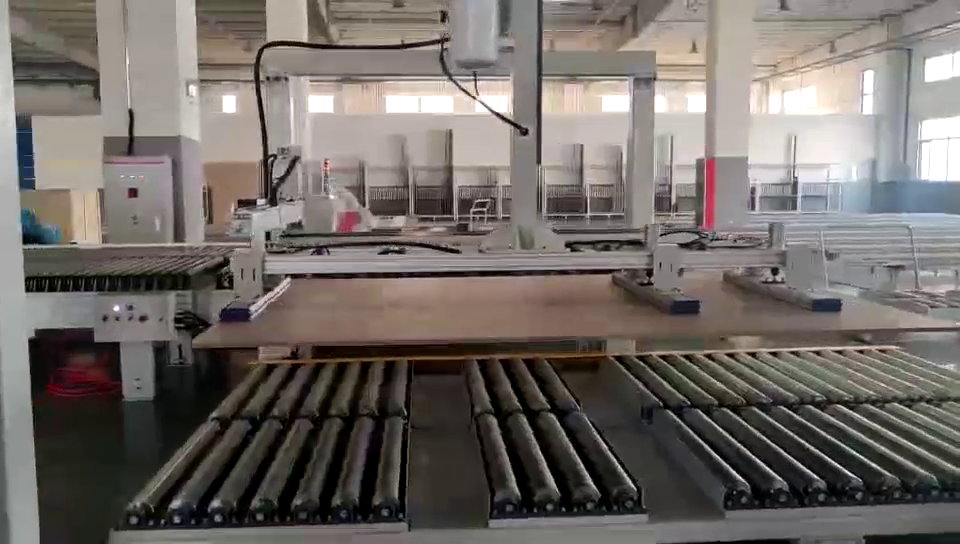
Automated crane material handling system
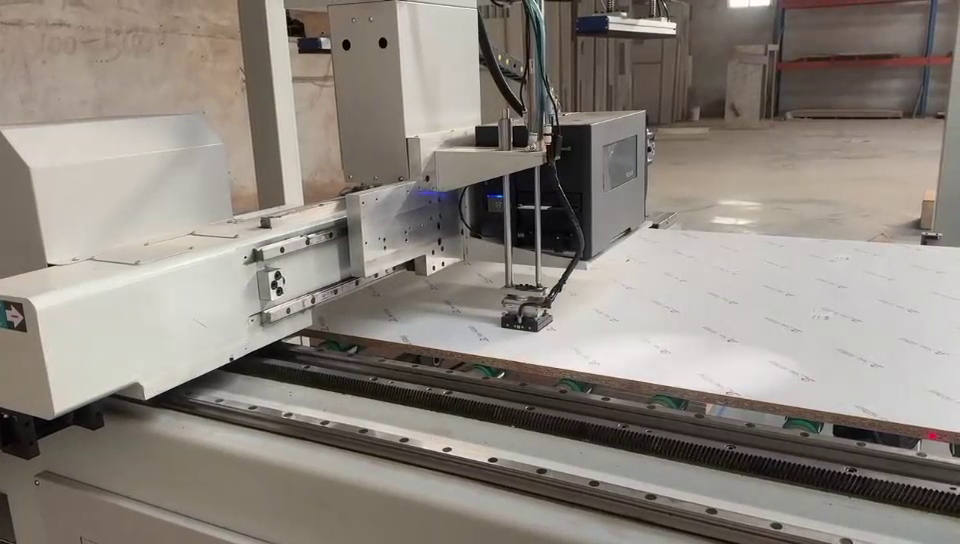
Intelligent upstream labeling integration
Our Production Line Automation systems typically deliver:
- 300-500% Increase in Per-Operator Production - Dramatically higher output without proportional labor increases
- 40-60% Cost Reduction - Compared to equivalent European automation systems
- 50-70% Reduction in Floor Space Requirements - Through vertical storage optimization
- 15-20% Reduction in Material Waste - Through optimized nesting and material selection
- ROI in 12-24 Months - For most high-volume manufacturing operations
What Our Clients Say
"After implementing their multi-CNC automation system with crane storage, our production capacity increased by 320% while our labor costs decreased by 40%. The system paid for itself in just 18 months and continues to give us a competitive edge in the market."— Michael Reynolds, CEO, Precision Millwork Inc.
"We compared automation solutions from Germany and Italy that were nearly twice the price of what Front Range CNC offered. Not only did we save significantly on the initial investment, but the system was customized specifically for our unique production requirements rather than being forced to adapt to a predetermined configuration."— Jennifer Watts, Operations Director, Modern Cabinet Systems
Frequently Asked Questions
Ready to Transform Your Production Capabilities?
Take the first step toward revolutionizing your manufacturing efficiency with Front Range CNC's Production Line Automation solutions designed specifically for your operation.